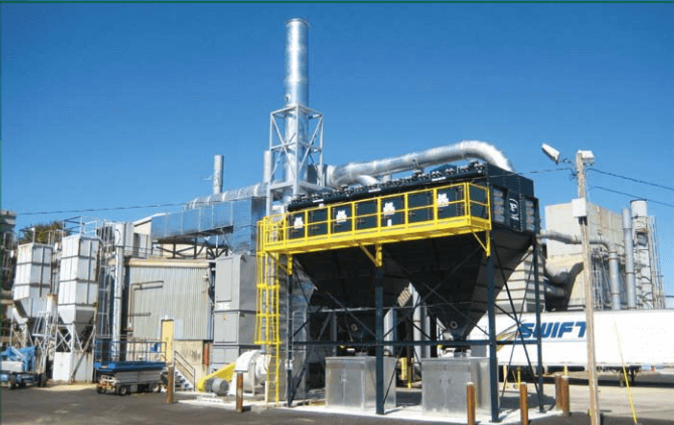
High Efficiency Vortex Scrubbers
Cyclo-Swirl vortex scrubbers offer high efficiency at low operating costs, equalling the performance of venturi scrubbers at 25% less pressure drop. They have no nozzles or moving parts, reducing maintenance time and costs. These scrubbers operate with 99% efficiency for various applications and micron sizes, with reduced efficiency for particles under 3 microns.
High efficiency vortex scrubbers, ’CYCLO-SWIRL’ with low operating cost, offers the performance equal to venturi scrubbers and works at 25% less pressure drop. There are no nozzles or moving parts eliminating time consuming and costly maintenance.
“CYCLO-SWIRL” operates in the 99% efficiency range for a wide variety of applications and over a wide range of micron sizes, with removal efficiency dropping off under 3 microns.
PRINCIPLE OF OPERATION:
The dirty air inlet is positioned tangentially which imparts centrifugal force for large particles to separate out, before the mixture is passed with high velocity through a fixed-position multi blade cage. The mixing of the dust-laden air stream and liquid occurs with increased turbulence, once the contaminated air/water is passed into the ‘multi-slot cage’, it creates atomized inner cyclonic vortex. These combined actions create the scrubbing efficiency.
The cleaned air is then made to pass up-wards, into the ‘vortex section’ where the cloud of fine water droplets are made to spin and separate out and the moisture contained clean air is directed into the ‘expansion chamber’ where the air velocity is reduced drastically, which provides the required contact time for removal of mist and any uncollected submicron particles before expelling the cleaned air.
The particulate material is collected within the conical bottom of the scrubber for the recovery or disposal. Water tank is normally located under the scrubber and the level is maintained automatically and make-up water is only needed to compensate for evaporation or sludge removal.
APPLICATIONS:
Food industry:
Serves the process requirement, such as the Filling, Weighing, Crushing, Roasting, Drying.
Chemical and Pharmaceutical industry:
Servers to abate the processes dust where Mixing, Palletizing, Crushing & Grinding, Sifting, Sieving, Drying, Weighing, Packing and Bagging are carried out.